This site recently ran fine stories about more sugar, soon on the market in North-western Europe; industry will process that to bioethanol and further to bioethylene, with ethylene oxide and ethylene glycol in its trail. That is the basis for the green chemical industry to make a take-off in Europe, entailing billions of investment. But this is not the final stage. These processes treat oxygen inefficiently: first kicked out, then brought back in. Fermentation technology will enable us to perform these reactions in one step, keeping the oxygen in place. But this technology is still in development. Allow the green chemistry some ten years to mature. A story form the chemical point of view.

Retain structure and function in green chemistry
The major advantage of green chemistry is that we can retain nature’s structure and function. In order to reap that advantage, we will have to retain all elements that constitute the plant (aside from carbon and hydrogen); oxygen in particular, that enters biomass by photosynthesis. And other valuable elements like sulphur, nitrogen and phosphorus. We push all that aside if we process sugars into bioethanol and that into ethylene: then we do not merely break bonds, but also remove the oxygen. It will have to brought back in again, in order to lead to chemical products. The conclusion should be that from a sustainability point of view, we should look for a direct pathway from ethanol (be it bio or not), or sugar, to ethylene oxide and ethylene glycol. The latter molecule contains two oxygen atoms, and that is a big bonus for the application of green chemistry on a large scale. Industry discovered that long ago when processing vegetal substances.
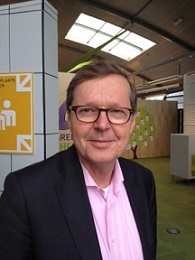
Classical chemistry
Let us have a look first at the sugars that will constitute the feedstock for green chemistry and the green chemical industry in the next 10 years; and at the present opportunities of this renewable feedstock.
– Processing C6 sugars to bioethanol already illustrates neatly the argument made above: in that step, we lose an appreciable amount of carbon and oxygen in the form of CO2. We could capture that (because it is quite pure and can be used for the production of beverages, in horticulture or in algae ponds). But it sells at a low price. About one half of the sugar disappears in the form of CO2: on paper, one needs almost 2 kg of sugars for the production of 1 kg of bioethanol. The equation for this reaction (with the mass balance in parentheses) is:
C6H12O6 (180) → 2 C2H5OH (92) + 2 CO2 (88)
I.e. 180 kg of sugars will produce at most 92 kg of ethanol. That is fine as long as sugar is cheap (for instance 250 Euro/ton), bioethanol sells at an adequate price (for instance >700 Euro/ton), or when the business case is supported by a subsidy (in cash or in the form of double counting of biofuels). The lifting of the sugar quota is the key to a lower price for sugars, an absolute prerequisite for large-scale business cases in the green chemical industry.
– The second step involves dehydration of bioethanol to bioethylene: here we lose oxygen once again, now in the form of water. We lose about 40% of bioethanol’s weight. The equation for this reaction (with the mass balance in parentheses) is:
C2H5OH (46) → C2H4 (28) + H2O (18)
By weight, the efficiency of this reaction chain from C6 sugars to bioethylene in these two steps is 56/180 x 100% = 31%. In short, we need at least 3 kg of sugars for 1 kg of bioethylene. In reality even a bit more than that, because reactions do not have a 100% efficiency in reality. We can do this if sugars are very cheap (for instance <230 Euro/ton), bioethylene sells at a high price (>1000 Euro/ton) or if there is a sufficiently high green premium on bioethylene (which often is not the case). Then we can imagine a business case in which we can start calculating Capex (investment costs), Opex (operational costs like energy but excluding feedstock costs) and profit margin. But there is no room for that if feedstock costs amount to 80-100% of revenues already.
– The third step consists of processing bioethylene to biobased ethylene oxide (EO) and further to biobased mono ethylene glycol (MEG). Here, we first add oxygen to (EO) and then water to (MEG). I.e. we process the base molecule ethylene to molecules with a higher functionality and molecular weight. At present, there is no commercially viable alternative for this pathway; Coca-Cola, too, obtains its biobased MEG for its Plant Bottle in this way. So for the time being, this inefficient pathway serves a big market.
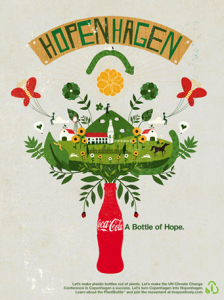
Direct fermentation
In green chemistry and the green chemical industry, this should of course be done differently; there are (at least) two alternatives:
1. Direct fermentation of sugars to biobased MEG (R&D, first IP published)
2. Catalytic processing of bioethanol to biobased EO (R&D, first IP published)
The (carbon) efficiency of the first pathway is quite fine. The equation for the reaction of sugars directly to MEG (mass balance in parentheses again):
C6H12O6 (180) + 3 H2 (6) → 3 C2H6O2 (186)
One kg of sugar will therefore produce more than 1 kg of MEG, if we have a source of hydrogen. As yet, we can only perform this reaction on a lab scale (MIT – Boston). But clearly, this is the direction into which to move forward. This could lead to innovation! But unfortunately, this development in green chemistry is mostly outside Europe.
Processing bioethanol to biobased ethylene oxide is done with noble metals catalysts. This line of research has clearly passed the proof of principle already. Check for instance: Direct conversion of ethanol to ethylene oxide on gold based catalysts. This research is done by a number of industries. Therefore, there is little to be found on it in the open access literature.
The upshot of these examples is that fermentation is crucially important for sugar processing. The pathway from sugars to bioethanol is not very favourable (of course, unless one would want to make Champagne or Cremant de Bourgogne…:-). Lactic acid from sugar is just fine, one kg of sugar will yield one kg of lactic acid. Succinic acid is perfect, in this pathway we also capture CO2, one kg of sugar will yield 1.3 kg of succinic acid.
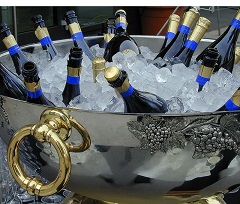
Lignin as a source of aliphatic and aromatic molecules
All this holds true too, for second generation sugars (C5-C6 sugars) derived from lignocellulose. The biorefinery step will also yield us lignin, in addition to sugars. Lignin comes in many forms and qualities. The overall structure formula is in the order of: (C10H12O3)n. So, lignin contains much more hydrocarbon than oxygen, compared to sugars. And it is highly aromatic. At present, most of it is incinerated, there are hardly any other applications yet. Prices depend mainly on quality, there is a wide range of 50-500 Euro/ton (50 Euro/ton for the ‘rubbish’, 500 Euro for special fractions like organosolve).
Pyrolysis of lignin may produce aromatic substances (just on a pilot scale, so far), preferably those containing oxygen, like phenols, alkylphenols etc.
Gasification at low temperatures may also produce aromatic compounds (ECN). Gasification at higher temperatures will produce syngas, leading to much loss of oxygen further down the pathway. Syngas can be processed to bioethylene, biopropylene and other hydrocarbons; either through Fischer-Tropsch (Shell, Sasol), or through MTO/MTG (Methanol to Olefins/Methanol to Gasolin) (ExxonMobil and others). The latter technology is comparatively old; it is applied commercially for methanol from syngas of fossil origin (coal, shale gas). These are energy intensive reactions, but starting from lignin and using heat integration and existing infrastructure, we might arrive at positive business cases, particularly if we can use cheap (albeit sulphur free) lignin.
In short
By way of conclusion, taking into account the time-to-market of the various technologies, we can foresee:
Present technology with GI Dynamics in the lead (see the interview with Ton Runneboom)
> 2020 first commercialisation of the new direct pathway from bioethanol to biobased EO. And on towards MEG, ethylene carbonate, acrylic acid or succinic acid anhydride, just to mention a few high-end building blocks
> 2020 alternative pathway to bioethylene from lignin, using gasification and MTO technology
> 2025 large-scale demo of the direct pathway from C6 sugars to MEG.
In short, allow green chemistry to develop another 10 years, and we will be able to build an efficient, fermentative chemical industry that uses sugars as its feedstock. A good cooperation between the fermentation sector and the smart green chemical sector will be a prerequisite for that.
As of 1 January, Willem Sederel was appointed chairman of the (Dutch) Biorenewables Business Platform. This is his first article since he was appointed in that capacity.