3D printing has the future. It will change the way in which we produce objects – maybe much less in factories and much more in shops around the corner. But so far, biobased materials have been difficult to 3D print. Most 3D printers use heat to melt the plastic or metal to be printed, and biobased materials then decompose. But cellulose nanofibrils offer a solution to this problem: the printing paste is wet and dries out to a solid structure.
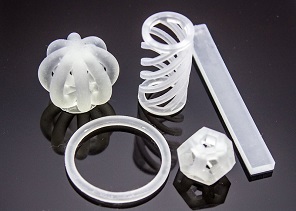
Cellulose nanofibrils (nanocellulose) are the smallest fibres into which we can decompose cellulose. They are made from wood or from the side streams of agricultural or food production; they are suitable for 3D printing pastes because an appropriate mix of cellulose nanofibrils and water is very viscous, and can contain much water, up to 50%. On drying out, these pastes produce mechanically very strong and biodegradable structures. The properties of the structure (moisture tolerance, rigidity and flexibility) can be modified through manipulation of the cross-links between the fibrils. Structures can now be made flexible, rigid and porous, and anything in between. Manufacturing a flexible structure out of bio-based materials is challenging, since the object tends to harden and become more rigid as it dries. ‘The drying process is critical,’ says professor Paul Gatenholm of Chalmers University in Gothenburg. ‘We have developed a process in which we freeze the objects and remove the water by different means as to control the shape of the dry objects. It is also possible to let the structure collapse in one direction, creating thin films.’
Cellulose nanofibrils 3D printing for medical applications
Another major institute that researches 3D printing with cellulose nanofibrils is VTT Technical Research Centre of Finland. They develop 3D printing technology for modifying textiles, mock-ups, indoor decoration elements and therapy applications in wound care. The first commercial applications will be seen in indoor decoration elements. Nanocellulose increases the opportunities for creating new surface patterns in decorative elements. But this development still requires light and moisture tests in various applications. And VTT develops 3D printing with cellulose nanofibrils for medical applications. The institute is currently developing a solution where a protein attached to a 3D-printed adhesive bandage can help to promote the growth of skin cells around a wound. The purpose is to have the healed wound area remain flexible instead of it developing stiff scar tissue. The development is done in collaboration with the University of Tampere and is funded by The Academy of Finland. This process can also be used in the cosmetics industry or in the manufacture of artificial bone. ‘By using nanocellulose, we have succeeded in creating 3D structures that absorb liquids three times more efficiently than the dressings commonly used in wound care,’ says VTT’s senior scientist Panu Lahtinen.
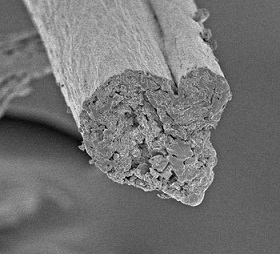
A further development is to produce electrically conductive structures using 3D printing and cellulose nanofibrils. At Chalmers University, they use carbon nanotubes for this goal. Using two gels together, one conductive and one non-conductive, and controlling the drying process, the researchers produced three-dimensional circuits; these provide a basis for the development of a wide range of products made by cellulose with in-built electric currents. ‘Potential applications range from sensors integrated with packaging, to textiles that convert body heat to electricity, and wound dressings that can communicate with healthcare workers,’ says Paul Gatenholm. At VTT, they develop precisely the latter technology. They combine the nanocellulose printed structure, a protein used in wound care, and printed electronics that measure wound healing into a single product. The structure wirelessly transmits temperature or bioimpedance data from the wound to a computer. Cellulose nanofibrils have not yet been approved for medical use, and therefore it will take several years before hospitals can use this application.
3D printing will revolutionise manufacturing
3D printing is a form of additive manufacturing that is predicted to revolutionise the manufacturing industry. It is an efficient method for complex, customised and light structures. The precision of the technology makes it possible to manufacture a whole new range of objects and it presents several advantages over older production techniques. The freedom of design is great, the lead time is short, and no material goes to waste. ‘Combining the use of cellulose to the fast technological development of 3D printing offers great environmental advantages,’ says Paul Gatenholm. ‘Cellulose is an unlimited renewable commodity and completely biodegradable.’ Cellulose nanofibrils can even be mixed with polypropylene to improve the processability of PP for 3D printing, and to enhance the mechanical properties of PP printed parts. 3D printing with cellulose nanofibrils opens up major opportunities for developing durable, biobased objects and materials.
Interesting? Then also read:
Wood fibres stronger than steel
Wood biorefinery has an enormous potential
A discovery that could lead to sustainable electronics
Fibres of the future: cellulosic fibres from wood