Recycling consumer products gets much attention. The circular economy calls upon us to cut down on waste and energy use and to stimulate recycling. Plastic recycling is in vogue. But rubber recycling is almost non-existent. Like recycling car tyres, which make up 80% of rubber consumption.
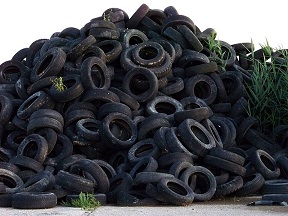
Rubber recycling is difficult
This month, the Dutch chemical magazine C2W ran an article on this subject (link in Dutch), written by Esther Thole. Why do we pay so little attention to rubber recycling, she wonders. For the volumes are big. Just in the Netherlands (pop. 18 million) some 10 million car tyres are discarded annually. Most are being landfilled or incinerated, world-wide. There is a certain interest in rubber recycling, but this is a difficult subject. Consequently, not much recycled material is being used in new tyres. Reuse does take place – but mainly in the form of downcycling. We use shredded tyres as a substrate in sporting grounds, dikes and roads. Or as a filter material. Not applications to be proud of in an industrial society.
The problem is that tyres consist of many materials. All tuned towards the function of the tyre in traffic, with disregard of possible recycling. The tread for instance consists of a rubber variety that differs from that of the sides. In addition to that, there are steel for firmness, textile for reinforcement and fillers like soot and silica. And a large number of additives. If we should start the recycling process with milling the tyre, we would end up with a fairly untreatable mixture of compounds.
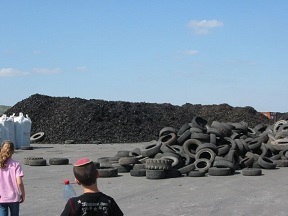
Environmental labels
And yet, rubber recycling isn’t a new subject for the tyre industry, says Wilma Dierkes of Twente University to C2W. For some thirty years already, the tyre industry adds some recyclate to new rubber production. But the amounts, then and now, are small. The recyclate’s quality is the bottleneck. The quality should improve, but this can only be done if the various fractions of the tyre would be separated right at the start of the process. Often, the tyre’s tread will consist of butadiene- and styrene/butadiene rubber, whereas the sides (‘cheeks’) often contain more natural rubber. For a proper process, these should be kept apart right from the start. The recyclate’s quality also requires the separation of fillers like soot and silica. And even if we should stick to those principles, ‘the result will never be of the same quality as the original,’ Wilma Dierkes tells C2W.
Moreover, separation right from the start is complicated by a lack of clarity on the tyre’s makeup. The EU requires environmental labels; these will tell you, more or less, the constituents of the tyre. But this is less clear if the tyre comes from abroad, especially when it comes from China. The ideal sorting process, says C2W, will read the label automatically. That will determine the entire process. But some labels are unclear; and foreign tyres often don’t carry such labels. How on earth could we then design an efficient rubber recycling process? And yet, this is the very problem that the researchers now try to tackle. Their goal is to design a process that can lead to a pilot plant. A plant fed with real, discarded tyres – and then see how far we come.
The interplay of regulation and technology development
Then, problems might just begin. Even if we should recover fairly uniform material streams from discarded tyres – how to proceed then? Most importantly, rubber should be devulcanized before it can be processed any further. Vulcanization is the process in which sulphur bridges are formed among polymer chains that still contain double bonds. Those sulphur bridges need to be broken down in order to obtain reusable new feedstock. Exactly that is what Wilma Dierkes and her team try to arrive at.
This technique of rubber recycling is being put to practice already – in the recycling of truck tyres. On those tyres, often a new tread is being mounted; this mainly consists of natural rubber. This will produce a fairly uniform product that can be devulcanized. If we apply this to motor car tyres, this will also break up some polymer chains. Dierkes’ group tries to prevent exactly that process. At the same time, they will have to prevent new chains from being formed. Ultimately, they hope to mix some 15 to 20% of the devulcanized product to ‘certain elements of the tyre’. That in itself would already be a major step forward, compared with the present state of affairs. And maybe those percentages could grow in the course of time.
Regulation or technology improvement
Their research has now reached the stage where it is ripe for putting the results to the test. Sorting, separation and devulcanization. Now the question arises if we should require factories to use these processes. Entrepreneurs are quite sceptical on the use of this kind of processes. For if eventually they should end up with a product of inferior quality, they might be held accountable.
C2W calls this a chicken-and-egg problem. Do we need regulation first, or technology? Technology should be in good order – and then the lawmakers need to be convinced that this is the case. But without regulation, the sector will not move. This clearly is one of the most difficult problems on the road to a circular society. But who knows? If we start now regulating rubber recycling, we might arrive in time at the target of a circular economy in 2050.
Interesting? Then also read:
Tyre recycling by devulcanisation
Dandelion rubber tyre developed by KeyGene, WUR and Vredestein
Biocomposites for cars