High dependence on fossil carbon, associated high carbon footprint, low recycling rates and microplastics: several solutions are emerging.
Written by Asta Partanen and Michael Carus. More information on the Cellulose Fibres Conference organized by nova-Institute on March 13 and 14 in Cologne: http://cellulose-fibres.eu.
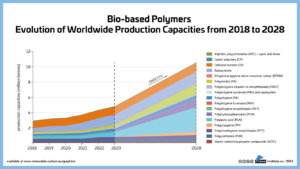
A dilemma
The evolution of the demand for textile fibres from 1960 to the present day (see figure 1 and table 1) shows how the textile industry found itself in this dilemma. In 1960, around 95% of textile fibres were of natural origin, from bio-based carbon, and there was no problem with microplastics, all fibres were biodegradable. The explosion in demand – 650% between 1960 and 2023 – could only be met by synthetic fibres from the chemical and plastics industries. Their share grew from 3% in 1960 to 68% in 2023 and from less than 700,000 tonnes to 85 million tonnes/year (The Fiber Year 2024). The new fibres covered a wide range of properties, could even achieve previously unknown properties and, above all, thanks to a powerful and innovative chemical and plastics industry, production volumes could be rapidly increased and comparatively low prices realised.
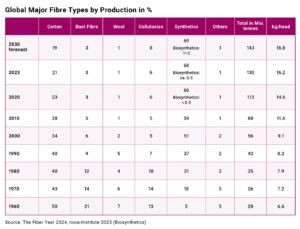
At the same time, sustainability has declined, the carbon footprint of the textiles has increased significantly and the issue of microplastics requires solutions. The first step would be to significantly increase the proportion of renewable fibres, as this is the only way to reduce dependence on fossil carbon, especially in the form of crude oil, and thus reduce the carbon footprint. But how can this be done? As defined by the Renewable Carbon Initiative, renewable carbon comes from biomass, CO2 and recycling: From carbon above ground. This addresses the core problem of climate change, which is extracting and using additional fossil carbon from the ground that will end up in the atmosphere.
What can cotton, bast fibres and wool contribute?
Cotton fibre production can hardly be increased, it is stagnating between 20 and max. 25 million tonnes/year. Cultivated areas can hardly be expanded, and existing areas are salinized by the irrigation required. With the exception of about 1% organic cotton, significant amounts of pesticides are used. The market share of “preferred” cotton – defined by a list of recognised programmes – will fall from 27% of total cotton production in 2019/20 to 24% in 2020/21, after years of growth. (Textile Exchange, October 2022: Preferred Fiber & Materials Market Report)
Bast fibres such as jute (75%), flax, hemp, ramie or kenaf would require a huge boost in technology development and capacity investment and will nevertheless probably remain more expensive than cotton, simply because bast fibres are much more complicated to process, e.g. separating the fibre from the stalk, which is not necessary for cotton as a fruit fibre. As a source of cellulose fibre, bast fibres will remain more expensive than wood.
Although bast fibres are more sustainable than many other fibres, there is unlikely to be a major change – unless China focuses on bast fibres as a substitute for cotton. Plans to do so have been put on hold due to technological problems. The importance of man-made cellulosic fibres (MMCFs) or simply cellulose fibres Cellulose fibre production has been growing steadily over the last decades, reaching an all-time high of nearly 8 million tonnes in 2023, and is expected to grow further to 11 million tonnes in 2030.
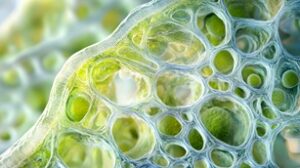
A wider range of properties
Cellulosic fibres are the only bio-based and biodegradable fibres that cover a wider range of properties and applications and can rapidly increase their capacity. The raw materials can be virgin wood as well as all types of cellulosic waste streams from forestry, agriculture, cotton processing waste, textile waste and paper waste. Increasing the share of cellulosic fibres will therefore play a crucial role in solving the sustainability challenges of the textile industry.
The production of MMCFs includes viscose, lyocell, modal, acetate and cupro. The market share of FSC and/or PEFC certified MMCF increased from 55–60% in 2020 to 60–65% of all MMCF in 2021. The market share of “recycled MMCFs” increased to an estimated share of 0.5%. Much research and development is underway. As a result, the volumes of recycled MMCFs are expected to increase significantly in the coming years. (Textile Exchange, October 2022: Preferred Fiber & Materials Market Report)
The CEPI study “Forest-Based Biorefineries: Innovative Bio-Based Products for a Clean Transition” (renewable-carbon.eu/publications/product/innovative-bio-based-products-for-a-clean-transition-pdf/) identified 143 biorefineries in Europe, of which 126 are operational and 17 are planned. Most of them are based on chemical pulping (67%) – the precursor of cellulose fibres. Most biorefineries are located in Sweden, Finland, Germany, Portugal and Austria. But there are already biorefineries in operation or planned in 18 different European countries.
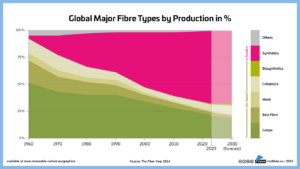
The global report “Is there enough biomass to defossilise the Chemicals and Derived Materials Sector by 2050?” (upcoming publication end of February 2025, available here: renewable-carbon.eu/publications) shows particularly high growth in dissolving/chemical pulp (from 9 in 2020 to 44 million tonnes in 2050; growth of 406%), cellulose fibres (from 7 in 2020 to 38 million tonnes in 2050; growth of 447%) and cellulose derivatives (from 2 in 2020 to 6 million tonnes in 2050; growth of 190%).
Biosynthetics – bio-based and CO2-based synthetic fibres
To further reduce the share of fossil-based synthetic fibres, bio-based polymer fibres (also called “biosynthetics”) are an excellent option because of their wide range of properties – only the implementation will take decades as the share today is only below 0.5%. There are many options, such as polyester fibres (PLA, PTT, PEF, PHA), polyolefin fibres (PE/PP), bio-based PA fibres from castor oil. PTT, for example, is well established in the US carpet market and PLA in the hygiene market. They are all bio-based, but only a few are also biodegradable (PLA, PHA).
Biosynthetics are one of many applications of bio-based polymers. In general, 17 bio-based polymers are currently commercially available with an installed capacity of over 4 million tonnes in 2023. Ten of these bio-based polymers are used as biosynthetics. resulting in the production of over one million tonnes of biosynthetics (nova report: Bio-based Building Blocks and Polymers – Global Capacities, Production and Trends 2023–2028.
In principle, many fibres can also be made from CO2, but here the technology and capacity needs to be developed, perhaps in parallel with the production of sustainable aviation fuels from CO2, which will become mandatory.
Circular economy – recycling of textile waste & fibre-to-fibre recycling
The textile industry is at a pivotal moment, where sustainability is no longer an option but a necessity. As the environmental impact of textile production and disposal becomes increasingly clear, the pressure to adopt circular economy principles is growing.
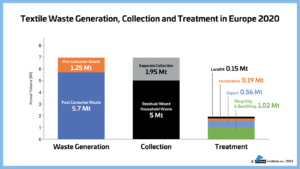
One promising solution is fibre-to-fibre recycling, a process that converts used textiles into new, high-quality fibres, effectively closing the waste loop. While significant progress has been made in the European Union, challenges remain, particularly in scaling up technologies, lack of collection systems and handling of mixed fibre textiles. Europe currently generates approximately 6.95 (1.25 + 5.7) million tonnes of textile waste per year, of which only 1.95 million tonnes is collected separately and 1.02 million tonnes is treated by recycling or backfilling (Figure 3).
The recycling of textiles reduces the demand for virgin fibres and the textile footprint. The share of recycled fibres increased slightly from 8.4% in 2020 to 8.9% in 2021, mainly due to an increase in bottle-based PET fibres. However, in 2021, less than 1% of the global fibre market will come from pre- and post-consumer recycled textiles (Textile Exchange, October 2022: Preferred Fiber & Materials Market Report). New regulations from Brussels for closed-loop recycling, especially bottle-to-bottle recycling, could threaten the use of bottle-based PET fibres in the textile industry. This would mean a reduction in recycling rates in the textile industry until the logistics and technologies are in place to recycle textiles on a large scale. This will be necessary to contribute to the circular economy. Several research projects are underway to find solutions and first pilot implementations are available.
The future of sustainable textiles
The sustainable textile industry of the future will be built on a foundation of cotton fibres and fast-growing cellulose fibres, later strongly supported by bio- and CO2-based synthetic fibres (“biosynthetics”), and high recycling rates for all types of fibres. This combination can eventually replace most fossil-based synthetic fibres by 2050.
Interesting? Then also read:
New biobased materials
Fibres of the future 2: cellulosic fibres from wood
Preservation of chemical complexity in green chemistry