Lignin valorization has become a top technological challenge. Lignin is one of the three main components of wood, the ubiquitous and carbon capturing resource. The other two are cellulose and hemicellulose. Lignin, accounting for 15-30% of woody biomass, is the least developed of these. Although the past fifteen years have seen a spectacular rise in lignin understanding, industrial applications don’t pop up. What are the problems and how do we find solutions?
This is the first of two articles on lignin processing. The articles appeared on August 15 and August 22, 2022.
An underutilized resource
In 2016, Utrecht University and Platform Agro-Paper-Chemistry issued a report ‘Lignin Valorization, The Importance of a Full Value Chain Approach’. It offers an excellent summary of recent research. Lignin, according to this paper, is a very interesting biopolymer. It has unique properties because of its highly aromatic nature and low oxygen content compared to cellulose and hemicellulose. It could make a very useful resource for renewable building blocks, fuels and materials. But although this resource is in ample supply, its isolation technology and treatment pose formidable problems.
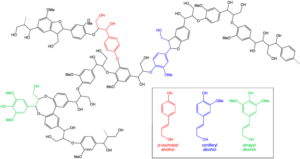
So far, these problems stood in the way of mass application of this material, except for heat production. The global pulp industry for instance produces 55 million tons of lignin each year, but the vast majority of this is burnt. As we can foresee that the era of fossil fuels is drawing to its end, proper lignin valorization has become important. But then, we should be able to isolate high-quality, useful lignin without compromising the quality of those other two main components. We will need to develop a proper wood biorefinery that valorizes all wood components. For it is often noted that ‘in order to create economically feasible biorefineries and overcome the initial energy cost associated with processing and pretreatment, all three major constituents should be fully valorized.’
A complex polymer
Lignin is a complex cross-linked polymer consisting mainly of coumaryl-, coniferyl-and sinapyl phenolic structures, also called monolignols. It is formed in the cell walls of wood or agricultural crops and plants, providing structural strength. But the term ‘lignin’ denotes a vast variety of substances. Their composition depends on the specific plant or tree species, the season, the climate and the plant age. Both the incidence of the most important building blocks and the ways in which they are linked together depend strongly on the plant species. Lignin monomers can connect in a number of ways (notably by direct carbon linking and the ether bond) and at different locations in the molecules.
To this variability, researchers and industries add their differences, owing to the processes used to treat the substance. We call the substances resulting from these treatment processes ‘technical lignins’. They differ from the original substance, and from each other, in characteristics like molecular weight, water solubility and degree of contamination (e.g. the incorporation of non-native elements, such as sulphur). As a result, also their physical and chemical properties vary. Properties like solubility in different solvents and molecular weight, greatly determine the possibilities for lignin valorization.
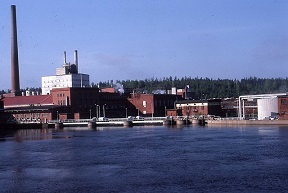
Industrial processes in lignin valorization
Industry uses a number of processes to treat wood as a resource. Often, these processes are not particularly suited for lignin valorization; cellulose (and to a lesser extent) hemicellulose are the main products. New processes however that may produce better quality lignin, tend to produce low-quality cellulose. Processes that deliver good qualities of all three main components haven’t yet been developed.
– Acidic pulping is done with sulphite or bisulphite and a hydroxide. The lignin ends up dissolved in the pulping liquor (black liquor) as lignosulfonate, together with some degraded carbohydrates. Most lignin obtained in this way is burnt in order to recover the chemicals.
– Alkaline pulping is done with sodium hydroxide, often together with sodium sulphide (Kraft process). Normally, the lignin in the black liquor is burnt for recovery of chemicals and energy production and thus not freely available. The Lignoboost process however, has been developed to isolate part of the lignin from black liquor in a rather pure way.
– The Bergius-Rheinau process uses concentrated hydrochloric acid and produces a highly insoluble technical lignin.
– In steam explosion processing, woody biomass is treated with steam at about 200oC and high pressure for a short period of time followed by a rapid decompression; this results in a quite native lignin though with significantly reduced molecular weight.
– Organosolv pulping involves biomass treatment at rather high temperatures with a mixture of water and an organic solvent like ethanol or acetic acid. The resulting lignin is quite well dissolvable.
– Hydrolysis of woody biomass will treat cellulose and hemicellulose and leave a residue of non-soluble lignin.
– Modern methods use Deep Eutectic Solvents (DES) or Ionic Liquids to dissolve wood in its entirety; treatment of such solutions may render valuable substances. However, no industrial process emerged from these attempts yet.
Applications
In principle, lignin can be extracted in a rather pure form and used as such. However, no industrial applications emerged so far. Much research is being done, but applications are ‘at early stages of development’. The other processes hardly produce lignin of commercial use, other than for incineration. For instance, of the technical lignin from the Kraft process, just 2% is commercially used for products, such as dispersing or binding agents. Lignosulfonates from the acidic pulping process are used more widely, for more or less the same purposes.
Applications include use as a dispersant; for instance in paints. As an emulsifier it is added to asphalt for preparation of temperature-stable emulsions. Lignins or products derived thereof are applied in plastics and foams. One producer (Borregaard) produces vanillin from lignin. Nevertheless, lignin remains a very underutilized resource.
Prospects for lignin valorization
In present wood treatment technologies, lignin is looked upon as a by-product; the main process is primarily intended to valorize cellulose. In principle, wood could be biorefined with an eye on valorizing the lignin component too. This would mean a complete overhaul of processes; in order to obtain lignin in an optimal functionality. Then, we could produce higher value compounds from it, including fine chemicals, building blocks for pharmaceuticals, flavouring agents and fragrances. The remaining lignin could still produce bulk chemicals and fuel additives, and finally a product that can be burnt. But in the short term, such processes are unlikely to be developed for commercial use.
It is hard to develop lignin valorization. Firstly, ‘lignin’ as such is very poorly defined. It differs chemically between species. Season, weather conditions and position in the field all influence the specific lignin makeup. On top of that, chemical treatment will also influence lignin’s molecular composition. There is a need for a databank listing all these varieties. The International Lignin Institute (ILI) gathers precisely such information. And there is a Lignin Club that unites lignin producers and customers world-wide. The club keeps score of a lignin matrix that shows what kind of lignin one will need for a specific application. And it oversees a major data base of lignin varieties and their properties. The foundation for lignin matchmaking.
Conclusion: the sector hopes that in the course of time, we will be able to produce commercial chemicals from this resource. And new applications (of rather pure lignin) may arise in the form of new materials made from the resource.
Written together with Alle Bruggink
The authors thank Annita Westenbroek for her comments on an earlier version of this article
Interesting? Then also read:
Respectful treatment of the complexity of biomass
Lignin makes a take-off across the board, says Ludo Diels (Vito)
Biobased economy is progressing quite well, says Annita Westenbroek
Wood biorefinery has an enormous potential