Lignin is the least abundant of the three main wood components. In the past two decades, much research has been done on lignin processing. It hasn’t resulted in major industrial processes yet. Shouldn’t we shift our focus?
This is the second of two articles on lignin processing. The articles appeared on August 15 and August 22, 2022.
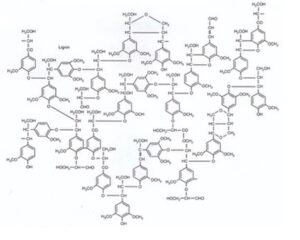
Lignin, a complicated substance
Paper and pulp industries produce a lot of lignin. For if we use the cellulose present in wood, we will end up with a pile of lignin. What to do with it? Cellulose-optimized processes tend to produce low-quality industrial lignin. Most of this is used for energy production. Meaning: it is burnt. Whereas lignin has a very interesting structure, inviting us to try and develop better applications from this feedstock.
But the great variety of bonds in lignin – both carbon-carbon bonds and ether bonds – presents us with problems from the very start. Soft decomposition methods, aimed at the ether bonds, will leave us with very stable side streams only fit for incineration. Harsher means, like high temperatures, will break down the entire structure and result in BTX (a mixture of benzene, toluene and xylenes); from which interesting substances will have to be reassembled. This looks like cracking crude oil; there, we can build petrochemical industry from simple substances. But lignin poses a lot of trouble. Often, a comparable procedure is not cost-effective here. In the end, just a few percent of lignin is being processed, the remainder is burnt.
New approaches
In recent years, scientists developed much more intricate procedures for lignin processing. Although we don’t yet seem to have reached the point where chemical treatment of wood becomes a profitable option. ‘Today,’ Hongli Zhu et al. write in Chemical Review), ‘a more holistic understanding of the interplay between the structure, chemistry, and performance of wood and wood-derived materials is advancing historical applications of these materials.’ They foresee ‘a myriad of new and exciting applications… (like) green electronics, biological devices, and energy storage and bioenergy.’ But so far, there are very few industrial applications.
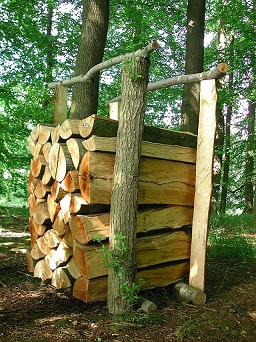
Zhuohua Sun et al. in Chemical Review confirm that valorization of components of lignocellulose is a challenge. But recently, they write, many creative strategies emerged that deliver defined products via catalytic or biocatalytic depolymerization in good yields. Owing to remarkable achievements in catalysis research, scientists succeeded in the production of well-defined compounds in acceptable quantities. They write that several of these pathways offer good prospects for future lignin processing. But again, although our knowledge has advanced a lot, commercial prospects do not seem to be around the corner.
Lignin, an attractive feedstock
Also Roberto Rinaldi et al. in Angewandte Chemie International Edition view lignin as ‘an attractive feedstock for targeted valorisation to fuels, polymer composites, synthetic building blocks and valuable (e.g., pharmaceutical) precursors.’ But ‘despite its potential as a raw material for the fuel and chemical industries, lignin remains the most poorly utilised of the lignocellulosic biopolymers.’ In order to valorize lignin effectively, we will need to fine-tune a number of multiple ‘upstream processes’ (i.e. lignin bioengineering, lignin isolation and ‘early-stage catalytic conversion of lignin’); and ‘downstream processes’ (i.e., lignin depolymerisation and upgrading). Again, in order to achieve this, we need an input and understanding from many scientific disciplines.
Remarkable among these disciplines is genetic engineering. It can be used to increase the homogeneity of the polymer, allowing for higher yields of targeted depolymerisation products; or to increase the proportion of easily cleavable linkages. This may open up new vistas for the future. But for now, we find no industrial applications of these processes.
Downstream lignin processing
As an example, let us follow this article in a specific section, Catalytic Downstream Processing Technologies, i.e. attempts to valorize the effluents of existing industrial processes. If processing conditions are not very severe, the problem is that lignin will decompose into quite complex compounds. If processing conditions are severe on the other hand, this will result in a mixture of many compounds; which we will need to separate, a technology in its own right.
An alternative would be the gradual depolymerisation of lignin over several stages. This will only be cost competitive if the products are in the order of fine chemicals, economically speaking; and even then, the profit might be offset by the cost of catalysts and reagents. And even if the pathway has been proven in principle, problems might still arise when it comes to upscaling production.
Lignin depolymerisation
The authors then go on to describe a ‘toolbox’ of lignin depolymerisation methods, operating under different severity conditions. Chemical depolymerisation will yield a mixture of chemicals that may be processed in further steps. The entire procedure is not unlike the treatment of crude oil, likewise producing different mixtures as reaction conditions vary. The difference being that cracking and further downstream processing of crude oil is well-researched; and has led to established procedures and equipment. Whereas lignin processing is in its infancy and still needs to be developed. Such a scheme would produce fine chemicals, bulk chemicals and a fraction that can only profitably be burnt.
Like the aforementioned authors, Brianna M. Upton and Andrea M. Kasko in Chemical Review look upon lignocellulosic biomass as the most accessible and renewable form of carbon. The most logical carbon-based feedstock for substitution of petroleum-based chemicals and materials. ‘The field of lignin-based polymeric materials and composites has seen great growth in the past 10 years, although the field still has room to grow…. The combination of these developments will allow not only for the synthesis of polymeric materials capable of competing with commodity commercial polymeric materials but also for the development of more sustainable synthetic practices.’ Again, the prospects are attractive, but the pathway remains studded with obstacles.
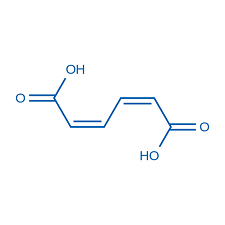
Biobased pathways
So far, we discussed catalytic pathways for lignin processing. But they might be overtaken by biobased procedures. Inspired by nature. Perhaps, Rinaldi et al. suggest, we should consult the way in which nature tackles such problems. Microorganisms tend to funnel a diverse feedstock to a small number of substances. One of the organisms that performs this trick is Pseudomonas putida, a soil bacterium. Under certain conditions, it can produce an attractive yield of cis,cis-muconic acid, a precursor of nylon-6,6. Other microorganisms perform comparable tricks.
‘Interesting about this research is that it copies nature, whereas nature hardly succeeds itself to break down the substance,’ says Bert Weckhuysen. He is professor in inorganic chemistry and catalysis at Utrecht University. ‘A dead tree will rot only very slowly, it may stay where it is for years. The important question being: can we improve breakdown done by nature?’
The wrong approach?
Particularly the catalytic approach to lignin processing seems to be reductionist in nature. Developed with petrochemical pathways in mind. If we could just break down the complicated resource to simple molecules, then in this concept we might be able to continue along well-known syntheses and arrive at more complicated and more valuable molecules. But maybe the entire concept is flawed. Maybe in this case the reductionist approach will not lead to economically viable pathways. Maybe a holistic approach might be much more fruitful. A procedure in which we move directly from one complicated structure to another one. ‘Traverse horizontally, or even better, transform the existing complexity into a higher one, with better or new applications.’
In spite of much work done by very clever scientists and institutions, lignin doesn’t yet seem to have yielded its secrets. Yes, our understanding has grown a lot. But applications of our reductionist approach don’t seem to multiply. Could lignin be proof of our growing insight that in some cases, the whole is better than the sum of its parts? Then, we might do better than attack the pile of lignin produced by the paper industry with a demolition hammer.
Lignin as a construction material
Lignin, according to Wikimedia Commons, fills the spaces in the cell wall between cellulose, hemicellulose, and pectin components, especially in vascular and support tissues. It plays a crucial part in conducting water and aqueous nutrients in plant stems. In contrast to cellulose and hemicellulose, lignin is hydrophobic; therefore, vascular tissue with a high proportion of lignin will conduct water efficiently. In addition to that, lignin is largely responsible for the strength of wood. Moreover, because it is chemically very stable, it is not very susceptible to pathogen attacks. Now all these functions will be important in structural materials used by mankind. Our use of wood as a construction material wouldn’t be possible without these properties. Wouldn’t we be able to make good use of them in pure lignin?
We know for instance that lignin has a different structure in various wood species. We can ‘traverse horizontally’ from softwood (where lignin contains many free hydroxyl groups) to hardwood by treating it with acetic anhydride or furfuryl alcohol. Another approach may be to develop new biorefinery concepts – although we know that this will take time. With them, we should be able to develop processes that yield marketable products from all three main components, including lignin. If we should drop the idea that we still will have to process lignin, we might very well arrive at a biorefinery concept yielding lignin as such (of a certain quality) as one of our end products. On the other hand, we might drop the idea of wood decomposition entirely; and end up with a multi-useful construction material, just by ‘traversing horizontally’.
Conclusion
Lignin has quite different properties in different trees and crops. If we intend to use lignin for structural purposes, we need to know more about its makeup. What kind of lignin has the best qualities for what kind of application? Can we alter lignin’s structure by genetic modification of the tree? Preferably producing a lignin that we can process better? Are there minor treatments with which we can tweak lignin’s properties to useful ones? Or should we shift our attention from lignin to wood – and concentrate on the opportunities of this construction material? There is a vast field here that we need to research. If we should just use a holistic approach instead of our traditional reductionist one.
Written together with Diederik van der Hoeven.
Interesting? Then also read:
Wood conservation
Mass timber, the new technology
Bio-bitumen for the roads of the future
I just love how many daring and “out-of-the-box” insights this blog has given me. Much more so than reading articles at top-notch peer-reviewed journals. Just want to thank you for sharing.