Lignin is often hailed as nature’s glue. It is the second most abundant polymer in the natural world. Found in plant cell walls, it plays a crucial role in providing structural support to plants. Up to now, if we isolate lignin, most of it is burnt for energy – we don’t have the technology to purify lignin and to put it to good use. But this is going to change.
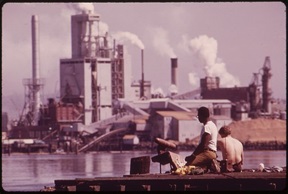
The Kraft process
In the Kraft pulping process (in use in 50 factories across Europe), lignin is dissolved in a hot solution of sodium hydroxide and sodium sulphide, and then separated from solid fibres. But the Kraft process is not very environmentally friendly. Byproducts include hydrogen sulphide, methyl mercaptan, dimethyl sulphide and dimethyl disulphide. The lignin is mainly burnt for energy. Lignin has such a high energy value that most pulp mills have a large surplus of energy.
But now, a Finnish biobased materials pioneer, LignEasy, has developed a method to refine and separate lignin into various kinds of liquid and solid products. These can be further tailored – depending on the end-use. This will unlock the potential of lignin use in a variety of industries. The pilot plant is still small, it is set to reach a production capacity of 1 ton/day later this autumn. But the implications may be large.
Innovating for sustainable material solutions
LignEasy aspires to reduce the carbon footprint associated with the pulping and chemical industries. Each year, over 15 million tons of lignin are burned by European Kraft pulp mills for energy. But LignEasy’s patented technology separates lignin for use in high-value applications such as plywood, construction materials, bio-components in plastics and packaging; providing sustainable alternatives to fossil-based products. This is important for instance in the sector of plastics. In this sector, achieving the net zero target by 2050 will require an annual production of 100-230 million tons of bioplastics; whereas present global production level is just 2 million tons.
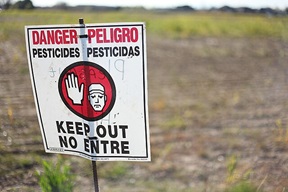
As the press release tells us: ‘Unlike existing lignin separation systems that can cause harmful sulphate discharge to the environment, LignEasy uses a sulphuric-acid-free separation technology and a novel filtration-based purification method. This innovation produces high-value lignin, reduces pulp mill emissions, and provides the chemical industry with a renewable feedstock in the form of an odourless, bio-based raw material available as liquid concentrate or dried powder. The lignin is ready for direct use in several products or possible chemical modification for an even broader range of applications.’
Chemical-free lignin
LignEasy’s process has as its end product a chemical-free lignin; this eliminates the need for environmentally harmful chemicals in the production process. Moreover, LignEasy contributes to the global shift towards sustainable practices. This supports environmental conservation and the growing demand for eco-friendly solutions.
Lignin holds a major potential for valuable bioproducts. It offers an eco-friendly alternative to traditional practices. The process reduces the carbon footprint of pulp manufacturing and the entire chemical industry. Towards ‘a greener and more sustainable planet’. This is strengthened by strategic partnerships with key players in the fields of research, development, and sustainable initiatives. Like RISE, the Research Institute of Sweden. And SciTech-Service Oy. And at LignEasy, they are constantly looking for new partnerships. ‘With organizations that share our dedication to revolutionizing industries, addressing climate change, and fostering a more sustainable world.’
Interesting? Then also read:
Lignin processing – challenges and limits
Difficulties in lignin valorization
Lignin makes a take-off across the board, says Ludo Diels (Vito)