The problem with plastics – aside from all the environmental issues they entail – is that they are excellent. It wouldn’t be a problem to wean ourselves off them if they weren’t great at what they do. Take PET for example – good barrier properties, crystal clear transparency and high recyclability, all at a low price point. Hard to beat – yet unfortunately also made with oil and gas-based feedstock and carrying intercontinental shipping emissions. The ever-increasing demand for this handy material means plastic production will account for 20% of global oil and gas consumption by 2050, creating a much rockier path to net zero. It is clear as plastic to see this is a problem that is going to get bigger unless we come up with a solution. So, what are our options?
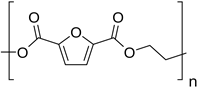
The realists in the room
Consumer behaviour is well-entrenched and our collective preference for plastic is rational due to its well-known advantages to maintain the integrity and quality of consumer goods, especially food and drinks. And it is not defeatist to say so, rather it is astute and respectful of the fact that consumers are responding to the legitimate advantages these materials and purchase models offer them.
So, what about a different approach? One which substitutes the material for a near-identical alternative with better environmental performance. Enter doppelganger PEF. Just one letter different from oil-based PET, but with game-changing potential for the plastics industry.
Sweeten the offer
We don’t need the oil-based route to PEF (polyethylene furanoate) because there is in fact a more elegant way to get to FDCA, a crucial component in PEF, specifically the ‘F’ part. Taking a step back for a leap forward always carries risk, but it has proven to be worth it. We now have a more controlled, highly customizable, yet less energy intensive process that can bring high quality, cost-effective FDCA and PEF a step closer to commercial development at scale.
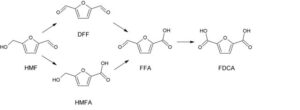
The advantages begin before we even get into the process, because we can make PEF out of biobased feedstocks, namely: sugar derived from industrial starch. Sugar is the simple but super-powered ingredient that is the basis for a major move away from the well-trodden path of oil-based feedstocks. This means we can create a more sustainable drop-in replacement for PET that doesn’t require polymer manufacturing, converting or recycling equipment to be changed.
A bioplastic above the rest
There is a huge range of oxygen-sensitive drinks that need effective bottles to preserve the integrity of the product, whether that is juice or vitamin drinks. This is where PEF comes in a cut above the rest – its gas barrier properties are many times better than PET. That makes it a particularly appealing option for brands who want to improve the sustainability of their products while increasing performance. The overwhelming majority of champagne and sparkling wines are currently served in heavy glass bottles that weigh more than the drinks they contain, adding hugely to transportation costs and emissions. Imagine a much lighter sustainable alternative that preserves that all important cork-popping ability, with an enhanced protection of the carbonated element of the drink, so consumers can get the full enjoyment from their products.
The applications for PEF are by no means limited to bottles. There is every form of tray and jar traditionally produced with PET that could benefit from the recyclable nature, strength, heat resistance, protective barrier properties, and transparency of packaging that consumers have come to expect, and PEF can provide. Looking to the future, it is continuous innovation with bioplastics that provides our best bet for a truly circular economy. This is the PEF-based products themselves, but also those desirable side products of its chemistry that have a promising future of their own.
Creating a circular economy
With the use of selective chemistry we are able to create the key intermediate HMF (hydroxymethylfurfural) from our sugar feedstock, which we can turn into a desirable end product through further sophisticated processes separate to the creation of PEF. HMF can be isolated and deployed in applications such as glues and paint, and its potential is vast. For example, there is already work being done to use HMF as a replacement for formaldehyde; and to combine it with other biomaterials such as lignin, derived from wood, to create binders for the construction industry.
This potential increases even more when we expand beyond sugar, to include a range of sustainable sources such as agricultural waste, recycled fibres and trees, and avoid an over-reliance on the starch needed for our food supply. A combination of those sources at scale can empower us to deploy HMF derivatives as a fuel additive in areas of transport proving difficult to electrify; such as shipping, long-distance trucking and aviation. We will be able to plug that biofuel gap and reap the sustainability benefits, while gaining the enhanced performance that we already see in bioplastic packaging. For those with the vision, HMF is not just a side product, or even a side product that can be turned into a tool, but a whole toolbox to be applied to sustainably serve a variety of humanity’s needs.
Imagine that world of a truly circular economy where you make a paper cup from tree fibre, it gets recycled and turned into a carton box used by Amazon to ship goods, and then gets recycled again until the point the fibre starts to break down. Now we don’t need to leave it there. We can break that down into sugar molecules, then transform it into bioplastic and start the process all over again in a way that is sustainable and performance-enhancing. It serves as a reminder that the race to create a doppelganger plastic began as a step in the right direction, but now we see that the process itself could precipitate a giant leap forward for the circular economy.
Dirk den Ouden is Vice President of Circular Chemicals at Stora Enso
Interesting? Then also read:
Wood conservation
Three development phases in green chemistry
Toward a global treaty on plastic pollution