Elk jaar gebruikt de Europese auto-industrie ongeveer 80.000 ton hout en plantenvezels om composieten te versterken, ter vervanging van synthetische vezels als glas en koolstofvezel. Biocomposieten zijn steeds meer populair geworden bij automakers omdat zij licht zijn, met hogere prestaties en lagere CO2-uitstoot tot gevolg. Ze worden gebruikt voor het binnenwerk: deur- en vloerpanelen, maar ze kunnen ook worden gebruikt voor dragende constructies.
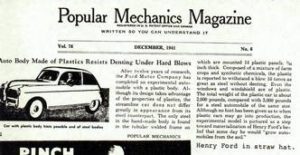
Biocomposieten in 1941
In 1941 kwam Henry Ford met een prototype, de ‘Soybean Car’ met een plastic opbouw die een derde minder woog dan een soortgelijke auto met stalen opbouw. De panelen waren, zo wordt verteld, gemaakt van een bioplastic op basis van soja, versterkt met natuurvezels. We weten nu niet meer precies hoe dit plastic in elkaar zat, maar men vermoedt dat het onder meer bestond uit sojabonen, tarwe, hennep, vlas en ramie. De oprichter van het Fordbedrijf dacht dat de plasticpanelen veiliger waren dan staal, en hij hoopte dat dit nieuwe materiaal staal zou gaan vervangen. Maar de Tweede Wereldoorlog maakte een eind aan zijn plannen. Toen de VS eind 1941 de oorlog verklaarden, werd de productie van auto’s stopgezet. Helaas leidde dit ook tot het einde van het Soybean Car-project, en kennelijk werd het prototype later vernietigd door de ontwerper van Ford, Lowell E. Overly.
Meer recent is het gebruik van kenafvezels door de Amerikaanse automaker in de sierstrippen op de deuren van de eerste generatie Mondeo’s; deze rolden van de band in 1993. En nu worden deze in alle auto’s van Ford gemaakt van een mix van tenminste 50% natuurvezels en plastic. Het bedrijf let goed op het duurzame en milieuvriendelijke karakter van deze materialen, maar het gaat ook om gewicht, zegt Maira Magnani, technicus bij het onderzoeks- en innovatiecentrum van het autobedrijf in Aken. Volgens haar komen biocomposieten alleen in aanmerking als zij hetzelfde of minder wegen dan de onderdelen die zij vervangen. ‘Want 80% van de footprint van de auto ontstaat bij het gebruik, en dat is direct verbonden met het gewicht’.
Kansen
Magnani zegt dat de nu geproduceerde Fords gemiddeld 9-18 kilo materialen bevatten afkomstig van groene of hernieuwbare grondstoffen. Het gaat daarbij vooral, maar niet alleen om plastics versterkt met vezels. De bandstofleidingen zijn bijvoorbeeld in de meeste modellen gemaakt van een plastic op basis van castorolie. In de binnenafwerking gebruiken autobedrijven de meeste biocomposieten, volgens Mike Clowry, adjunct-directeur van de ontwikkelafdeling van de International Automotive Components Group (IAC). ‘We hebben kaartenhouders, afwerking van achterbak en achterbank, en onderdelen van deuren gemaakt van composieten met natuurvezels,’ zegt Clowry. ‘In 2017 heeft IAC de ‘eerste lijst voor een zonnedak gemaakt van composieten met natuurvezels’ gemaakt, dat bestaat uit 70% vezels van hennep en kenaf, en 50% minder weegt dan een metalen lijst. Deze wordt nu gebruikt in alle Mercedes Benz E- en A-klasse auto’s.
Hom Dhakal, onderzoeker van composietmaterialen aan de Universiteit van Portsmouth in het VK, denkt dat de volgende stap zal bestaan uit het maken van niet-dragende buitendelen, ‘als voor- en achterbumper van vlasvezelcomposieten’. Hij zegt dat zij team al bijna een vlasvezelcomposiet heeft gemaakt dat voldoet aan de mechanische materiaaleisen die de meeste autofabrikanten stellen aan motorkappen. Zij zouden nu al aan die eisen kunnen voldoen door bijvoorbeeld glasvezels toe te voegen aan de mix, maar dat zou ten koste gaan van de duurzaamheid, en recycling van het materiaal moeilijker maken, zegt hij. Dit is het grootste struikelblok voor constructief gebruik van biocomposieten: hen echt duurzamer te maken dan de alternatieven. Je moet om dit op te lossen, kijken naar het productieproces, zegt Dhakal. ‘Bij een efficiënt proces gebruik je minder energie en minder materiaal.’ Dit spaart tijd en geld, en verbetert de duurzaamheid. Als de betere productietechnieken eenmaal zijn doorgebroken, zullen ook biocomposieten doorbreken voor niet-dragende buitendelen, denkt Dhakal. Hij denkt dat verlaging van de uitlaatnormen door de Europese Unie belangrijk is geweest voor het gebruik van lichtere materialen als natuurlijke vezelcomposieten. In 2021 moeten nieuwe auto’s 40% minder uitstoten dan gemiddeld in 2007. En de EU overweegt verdere emissiereducties voor 2030.
Lagere koolstoffootprint voor biocomposieten
Het maken van natuurlijke vezels vraagt ook minder energie dan dat van synthetische vezels. Volgens een analyse van nova-Instituut ontstaat een uitstoot van 1,7-2,2 ton CO2-equivalent per ton glasvezel, tegenover 0,5-0,7 ton CO2-equivalent voor vier natuurvezels – vlas, hennep, jute en kenaf. Een Indiase studie kwam tot vergelijkbare cijfers voor deze vezels; de koolstoffootprint voor natuurlijke vezel komt op 20-50% lager dan voor glasvezel. Maar deze cijfers gelden alleen tot aan de fabrieksdeur; ze vertellen nog niets over de footprint bij het maken van de auto met de composieten, en het rijden ermee.
In 2004 vergeleek een veelgeciteerd overzicht de levenscycluskosten van natuurlijke en glasvezelcomposieten. De conclusie was dat natuurlijke vezelmaterialen waarschijnlijk beter waren voor het milieu dan glasvezels, in de meeste toepassingen. Volgens de auteurs zijn natuurlijke vezels lichter en is er minder energie nodig om deze te maken; en bij biocomposieten worden minder vervuilende polymeren gebruikt dan bij glasvezelcomposieten. En ze zeggen nog eens dat bij gebruik van natuurlijke vezels in auto’s vooral het lagere gewicht belangrijk is: het rendement van de motor gaat omhoog, en de uitstoot omlaag.
Dit artikel werd oorspronkelijk gepubliceerd op de site van allthings.bio.
Interessant? Lees dan ook:
Groene materialen in de auto, deel 1: de eisen van de automobielindustrie
Groene materialen in de auto, deel 2: de plannen van de groene industrie
Recycling van autobanden door devulkanisatie